Comment prévenir efficacement les risques d’écrasement au travail ?
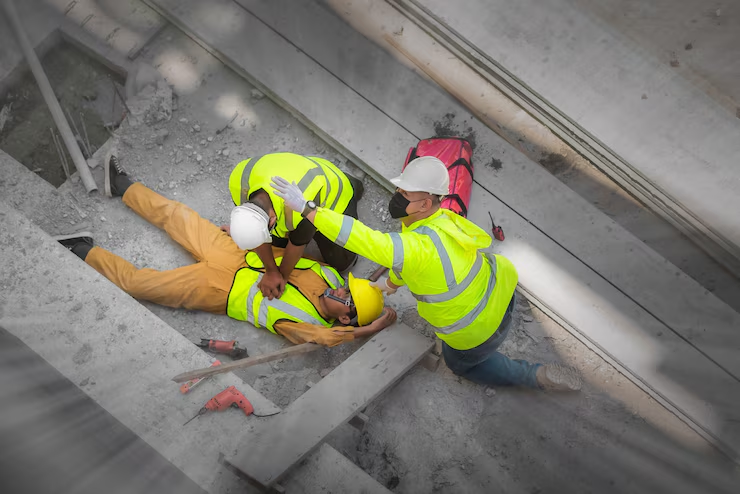
Chaque année, les accidents par écrasement au travail provoquent des blessures graves, des incapacités permanentes et des décès dans les cas les plus dramatiques. Trop souvent sous-estimés, ces risques concernent une grande variété de métiers, de l’ouvrier du BTP à l’opérateur logistique, en passant par le technicien de maintenance ou le cariste.
Les situations à risque sont nombreuses : machines mal sécurisées, engins en mouvement, charges instables, manœuvres mal coordonnées ou encore espaces de travail exigus dans lesquels cohabitent hommes et équipements. Dans ces contextes, un instant d’inattention, un défaut d’organisation ou une défaillance technique peut suffire à provoquer un accident aux conséquences irréversibles.
Face à ces enjeux, la prévention ne peut se contenter de dispositifs isolés. Elle doit s’inscrire dans une démarche globale de gestion des risques : repérage des zones critiques, formation régulière des équipes, usage d’équipements adaptés, et intégration des nouvelles technologies pour anticiper plutôt que réparer.
Ce dossier explore en profondeur les différentes facettes de ce risque professionnel individuel. Sans se substituer à une analyse terrain, il propose des clés de compréhension et d’action pour réduire les risques d’écrasement sur les lieux de travail.
Les risques d’écrasement liés aux chutes d’objets
Dans de nombreux environnements professionnels, les chutes d’objets constituent un risque majeur d’écrasement, souvent sous-évalué dans les plans de prévention. Qu’il s’agisse d’un outil manipulé en hauteur, d’une palette stockée à des dizaines de mètres du sol ou d’un équipement suspendu mal sécurisé, la chute d’un objet lourd ou même modérément massif peut provoquer des lésions sérieuses allant jusqu’à la perte de connaissance, des traumatismes crâniens ou des fractures ouvertes.
Ces drames touchent particulièrement les secteurs du BTP, de la maintenance industrielle, du spectacle vivant ou encore de la logistique.
Outils manipulés en hauteur : des projectiles involontaires
Quand on travaille en hauteur, sur une toiture, une façade, un pylône ou un échafaudage, les outils deviennent des compagnons de tous les instants. Perceuse, marteau, clé, cutter… On les attrape, on les pose, on les repose, parfois à la hâte. Mais dès qu’un outil échappe des mains ou glisse d’une surface, il devient un projectile avec des conséquences parfois graves.
Une simple clé tombée de quelques mètres peut atteindre une personne située en contrebas avec une force capable de percer un casque ou de fracturer un os. Ces accidents sont d’autant plus redoutables qu’ils sont silencieux, soudains… et évitables.
Une problématique bien réelle : un outil qui tombe, c’est un danger en chute libre
Même avec un casque, un travailleur exposé à une chute d’outil n’est jamais totalement protégé. Pourquoi ? Parce que la vitesse et l’énergie accumulées par l’objet pendant la chute peuvent suffire à provoquer
- Un traumatisme crânien
- Une blessure à l’épaule ou au cou
- Dans le pire des cas, un accident grave voire mortel
Et ce risque ne concerne pas uniquement les grands chantiers.
Les bonnes pratiques pour éviter les chutes d’outils
Heureusement, il existe des solutions simples, efficaces et éprouvées pour éviter ce type d’accident.
1. Utiliser des ceintures porte-outils avec fixations sécurisées
Plutôt que de poser ses outils à même la structure ou dans une poche de veste, chaque ouvrier doit être équipé d’une ceinture adaptée, dotée de
- Passants renforcés pour insérer les outils de manière stable
- Systèmes de blocage pour éviter les chutes au moindre mouvement
L’objectif d’un tel accessoire : que chaque outil ait sa place… et qu’il y reste.
2. Fixer les outils avec des longes anti-chute
Certains outils doivent rester attachés au harnais, à la ceinture ou à un point fixe, à l’aide de longes rétractables ou à enrouleur, voire de câbles souples avec mousquetons ou attaches sécurisées.
Ces dispositifs permettent d’utiliser les outils librement tout en étant immédiatement retenus en cas de lâcher accidentel. Avec une longe bien installée, lorsqu’un outil tombe, il ne touche jamais le sol.
3. Délimiter les zones de travail au sol
Lorsqu’un poste en hauteur est actif, il est impératif de
- Interdire l’accès aux zones situées juste en dessous
- Les baliser visiblement avec rubalises, cônes ou panneaux
- Informer les équipes au sol des risques liés à l’activité en hauteur
Personne ne doit circuler sous une zone où des outils sont utilisés… sauf en cas de nécessité clairement encadrée.
4. Organiser la coactivité : sol et hauteur doivent travailler ensemble
Les accidents surviennent souvent par manque de coordination. Il est donc essentiel de
- Mettre en place un plan de prévention de coactivité
- Définir les règles de communication entre les équipes en hauteur et celles au sol
- Désigner un référent sécurité pour superviser les zones sensibles
Une équipe qui se parle, c’est une équipe qui se protège mutuellement.
Objets suspendus : anticiper le danger venu d’en haut
Certains équipements, bien qu’immobiles à première vue, peuvent représenter un risque réel lorsqu’ils sont suspendus durablement en hauteur. Projecteurs de salle, portiques, moteurs de portes industrielles, enseignes, panneaux ou équipements sportifs fixés au plafond… autant d’éléments qui peuvent sembler stables jusqu’au jour où une fixation lâche.
Même si ce type d’accident est rare, ses conséquences peuvent être gravissimes, car quand un objet lourd tombe de plusieurs mètres, ni le casque, ni les réflexes ne suffisent.
Une menace silencieuse : quand la défaillance devient mortelle
Dans les hangars, les gymnases, les entrepôts, les parkings couverts ou les scènes d’événements, on oublie parfois que ce qui est suspendu… peut tomber. Et les raisons sont multiples
- Vibrations répétées (moteurs, souffleries, machinerie en fonctionnement)
- Fatigue des matériaux au fil du temps (câbles, crochets, fixations)
- Pose initiale non conforme ou insuffisamment documentée
- Entretien irrégulier ou inexistant
Le risque est encore plus élevé quand ces objets sont suspendus au-dessus de zones de passage, d’activités ou de postes de travail.
Les mesures de sécurisation essentielles
Pour éviter tout accident lié à une chute d’objet suspendu, la prévention technique et organisationnelle est indispensable.
1. Installer des systèmes antichute de charge
Un système antichute de charge est un dispositif de retenue qui prend le relais en cas de rupture de la fixation principale. Il peut s’agir de câbles de sécurité, de chaînes secondaires ou de systèmes à enroulement bloquant.
Ces dispositifs ne remplacent pas l’attache principale, mais en assurent la sécurité en cas de rupture. Ils doivent être dimensionnés pour la charge réelle, posés conformément aux normes et ne jamais être négligés sur du matériel lourd ou en hauteur permanente.
2. Réaliser des contrôles périodiques des fixations
Comme pour tout matériel technique, l’usure ne se voit pas toujours à l’œil nu. D’où l’importance d’une vérification régulière
- Des systèmes de fixation (crochets, chevilles, boulons, platines)
- Des câbles et suspentes (tests de tension, recherche de corrosion ou d’effilochage)
- Des structures porteuses elles-mêmes (fissures, affaissements, déformations…)
3. Mettre en place un plan de maintenance préventive
Prévoir, plutôt que réparer : telle est la clé de la sécurité durable. Cela passe par
- La création d’un registre de maintenance dans lequel est listé chaque point à vérifier
- La planification des interventions régulières (mensuelles, trimestrielles, annuelles)
- La traçabilité de chaque opération : qui a vérifié, quand et avec quel résultat
C’est ce suivi rigoureux qui permet de détecter un problème avant qu’il ne se transforme en accident.
4. Interdire l’accès sous les objets suspendus pendant les manipulations
Lorsqu’un équipement suspendu est installé, retiré ou ajusté, personne ne doit se trouver en dessous, même brièvement. Cela inclut les techniciens eux-mêmes. Une zone de sécurité doit être matérialisée autour, avec signalisation visible et balisage.
Échafaudages : un espace de travail doublement exposé
Travailler sur un échafaudage, c’est être suspendu entre ciel et sol, avec des risques de chaque côté. Que ce soit pour monter une façade, réparer une charpente ou installer une structure, les échafaudages (qu’ils soient fixes ou roulants) sont incontournables.
Mais ils peuvent rapidement devenir des sources de danger, non seulement pour ceux qui y travaillent, mais aussi pour ceux qui circulent en dessous. Un tournevis oublié, une planche mal calée, une bourrasque de vent… et c’est un objet qui tombe à toute vitesse et devient un projectile.
Deux niveaux de risque bien distincts… mais liés
Travailler en hauteur, c’est affronter un double danger : le risque de tomber soi-même… et celui de faire tomber quelque chose. Sur un échafaudage, ces deux risques sont étroitement liés et doivent être pris en compte ensemble pour garantir la sécurité de tous, en haut comme en bas.
1. Chute de matériaux ou d’outils laissés sur les plateformes
Il suffit de laisser un outil sans retenue, de le poser au bord d’une planche ou sur une surface inclinée pour qu’il tombe au moindre choc ou déplacement. Marteaux, visseuses, boulons, planches : tout ce qui n’est pas fixé devient un projectile potentiel.
2. Absence de protection latérale
Sans filet, garde-corps ou bâche, les objets peuvent glisser sur les côtés ou être poussés accidentellement. Si une personne passe juste en dessous, le moindre objet peut faire des dégâts, même avec un casque.
Les solutions techniques pour sécuriser le haut… et le bas
Heureusement, il existe des moyens simples et efficaces pour rendre l’environnement de travail plus sûr, aussi bien pour ceux qui travaillent en hauteur que pour ceux qui circulent à proximité.
1. Poser des filets de sécurité horizontaux
Ces filets sont tendus sous les niveaux de travail pour intercepter les objets qui tombent avant qu’ils n’atteignent le sol, créer une barrière visuelle qui rappelle le risque et incite à la prudence.
Ils doivent être
- Solides et conformes aux normes de sécurité
- Installés correctement (tension, fixation, dimension)
- Vérifiés régulièrement pour éviter les affaissements
2. Installer des filets verticaux ou des bâches latérales
Pour empêcher les chutes latérales d’outils ou de débris, il est recommandé de
- Fixer des filets verticaux ou des bâches de protection tout autour de l’échafaudage
- Bien couvrir les angles et les points de passage
- Choisir des matériaux résistants au vent et aux conditions extérieures
Ces protections créent un mur de sécurité entre la plateforme de travail et les passants ou les collègues en contrebas.
3. Délimiter les zones au sol à risque
Il est interdit de circuler sous une zone de travail en hauteur sans protection. Pour cela, on doit :
- Mettre en place des rubalises visibles tout autour de la zone
- Utiliser des barrières mobiles pour bloquer l’accès
- Afficher des panneaux clairs indiquant « interdiction temporaire de passage », « danger de chute d’objets », etc.
Cette zone doit être clairement identifiée, respectée et surveillée.
4. Former les équipes à l’organisation du poste de travail
Une bonne prévention passe aussi par les bons réflexes au quotidien. Il est essentiel de former les intervenants à :
- Ne jamais laisser d’outil non sécurisé sur les plateformes
- Utiliser des ceintures porte-outils ou des longes
- Ranger régulièrement le poste de travail pour éviter l’accumulation d’objets mobiles
Chaque travailleur doit devenir acteur de sa propre sécurité… et de celle des autres.
Rayonnages et racks : chute de palettes et charges mal stabilisées
Dans les entrepôts, les zones de stockage en hauteur ou les réserves logistiques, les racks et les rayonnages métalliques sont partout. Ils permettent d’optimiser l’espace et de ranger des charges parfois très lourdes sur différents niveaux. Mais mal utilisés ou mal entretenus, ils deviennent des sources de danger silencieuses.
Une palette mal posée, un montant tordu, une manœuvre mal maîtrisée avec un chariot… et c’est une charge de plusieurs dizaines de kilos qui tombe, pouvant blesser gravement une personne ou provoquer un effondrement en chaîne.
Les principales problématiques à surveiller
Les rayonnages en hauteur sont pratiques… mais pas sans danger. Pour éviter les accidents, il est essentiel de connaître les situations à risque les plus courantes et de les repérer à temps.
1. Chutes de charge liées à une mauvaise répartition
Quand une palette est trop lourde d’un côté ou mal positionnée sur les longerons, elle peut basculer au moindre choc. Une manœuvre brusque avec un chariot élévateur ou un transpalette peut suffire à tout faire tomber.
2. Détérioration des structures par choc
Un chariot qui percute un montant ou une traverse de rack (même légèrement) peut affaiblir la structure. Ce défaut, souvent invisible au premier regard, peut finir par provoquer un affaissement ou une chute de niveau.
3. Effondrement partiel d’une zone de stockage
En cas de surcharge, de choc ou de faiblesse structurelle non détectée, une portion du rayonnage peut s’effondrer brutalement et entraîner les charges posées dessus… et mettre en danger toute personne présente à proximité.
Les mesures de prévention efficaces à mettre en place
Face aux risques identifiés, la prévention ne doit rien laisser au hasard. Voici les solutions à privilégier.
1. Installer des filets ou grilles de rétention à l’arrière
Les filets anti-chute ou grilles métalliques de fond permettent de
- Retenir les palettes ou cartons qui glisseraient vers l’arrière
- Éviter qu’une charge ne tombe dans une allée ou sur un poste de travail
- Protéger les piétons et les opérateurs qui circulent derrière les racks
2. Renforcer la structure contre les chocs
On ne peut pas empêcher tous les accrochages, mais on peut protéger les zones les plus exposées avec des
- Sabots de protection fixés au sol autour des pieds des racks, qui absorbent les impacts légers sans affecter la structure
- Butoirs et arceaux anti-chocs pour guider les chariots et limiter les erreurs de trajectoire
- Plaques de renfort ou poteaux renforcés sur les angles
Il est préférable de protéger la structure plutôt que de la réparer après un accident.
3. Contrôler régulièrement l’état des racks
Un simple contrôle visuel peut suffire à repérer un montant tordu, un boulon desserré ou une traverse mal emboîtée. Il est donc important de
- Effectuer un tour quotidien par les équipes terrain
- Réaliser une vérification hebdomadaire ou mensuelle par un responsable maintenance ou sécurité
- Tenir un registre de contrôle avec date, observations et actions correctives
4. Former et sensibiliser les caristes
Les conducteurs de chariot ont une responsabilité directe dans la sécurité des rayonnages
- Ils doivent être formés à l’équilibrage des charges, à la stabilité des palettes et aux limites de capacité par niveau (exprimées en kg)
- Ils doivent savoir identifier un rack fragilisé ou signaler une structure endommagée
- Une sensibilisation régulière (causerie, affiche, rappel visuel) permet d’ancrer les bons réflexes
Les risques d’écrasement liés aux objets en mouvement
Contrairement aux machines industrielles ou aux véhicules lourds, certains objets en mouvement paraissent inoffensifs à première vue. Pourtant, leur chute ou leur déplacement accidentel peut entraîner des blessures par écrasement, en particulier au niveau des mains et des pieds. Ce type de risque concerne une grande variété d’activités quotidiennes : manipulation de charges à la main, manutention légère, fermeture de portes, circulation d’équipements roulants.
Ces risques sont souvent liés à une combinaison de facteurs : manque d’équipements de protection individuelle, environnement mal organisé, gestes précipités ou inattention passagère.
Objets qui tombent des mains : des accidents souvent évitables
On a tendance à sous-estimer les risques liés à la manipulation d’objets dits “courants” : cartons, outils, seaux, câbles, briques… Pourtant, ce sont souvent ces petites charges du quotidien qui causent les blessures les plus fréquentes, notamment aux pieds et aux mains, deux zones particulièrement exposées.
Il suffit d’un faux mouvement, d’une perte d’équilibre ou d’un objet mal calé et l’accident survient. Une simple chute de quelques kilos peut provoquer des traumatismes douloureux et invalidants. Et ces accidents sont d’autant plus frustrants, car on peut parfaitement les éviter.
Exemples concrets de situations à risque
Les dangers ne viennent pas toujours de grosses charges, mais plutôt de gestes répétitifs et de manipulations mal sécurisées. Voici quelques situations fréquentes
- Cartons transportés sur une ligne de production ou en logistique qui glissent ou sont mal posés
- Outils posés temporairement sur un établi ou un bord de table qui tombent sur une main au moindre choc ou faux geste
- Parpaings, seaux de mortier ou sacs de matériaux qu’on lâche par fatigue ou parce qu’on trébuche sur un chantier
- Bobines de câbles ou rouleaux instables qui roulent, basculent et se coincent dans les pieds
Dans chacun de ces cas, le pied et la main sont en première ligne.
Quels sont les risques principaux ?
Même une petite chute d’objet peut causer des dégâts importants, en particulier sur les extrémités, souvent moins protégées ou négligées. Cela peut
- Écraser des orteils ou le dessus du pied et provoquer
- Contusions douloureuses
- Fractures (même avec un petit objet mal positionné)
- Lésions ligamentaires ou tendineuses
- Coincer les doigts ou la main et provoquer
- Pincements, hématomes
- Entorses, luxations
- Un arrêt de travail prolongé dans certains cas
Ces blessures peuvent sembler bénignes, mais elles sont douloureuses, longues à guérir et facilement évitables avec de bons gestes et le bon équipement.
Quelles solutions concrètes mettre en place ?
Pour éviter qu’un simple outil ou un carton mal tenu ne devienne la cause d’une blessure sérieuse, il est essentiel de miser sur la prévention. Cela passe par un bon équipement et des gestes maîtrisés.
1. Porter des chaussures de sécurité adaptées
Le port de chaussures de sécurité normées est essentiel, même pour des tâches simples. Selon le type d’environnement
- S1P : idéale pour les milieux secs, avec coque anti-écrasement et semelle anti-perforation
- S3 : recommandée pour les environnements humides ou extérieurs (chantiers) avec résistance à l’eau, semelle antidérapante et protection renforcée
Une bonne chaussure de sécurité absorbe les chocs et protège les orteils, même en cas de chute d’objet lourd.
2. Utiliser des gants de protection adaptés
Les mains sont des outils précieux… mais fragiles. Pour les protéger, il faut opter pour des gants anti-chocs avec renforts au niveau des métacarpes et des phalanges. L’idéal est de choisir un modèle qui allie protection, souplesse et confort pour éviter les gestes maladroits.
3. Former les équipes aux bons gestes de manutention
Les gestes techniques mal maîtrisés sont souvent à l’origine des accidents. La prévention passe par la formation
- Bien saisir les objets (avec les deux mains, sans torsion)
- Stabiliser avant de poser ou de soulever
- Ne jamais porter plus que nécessaire
- Demander de l’aide ou utiliser des aides mécaniques quand le volume est encombrant
Des gestes simples, appris et répétés, réduisent considérablement les accidents.
4. Éviter les mauvaises habitudes de stockage
Un bon réflexe : ne jamais poser un objet instable ou lourd en hauteur, ni en déséquilibre.
- Préférer un stockage au sol ou à hauteur de main, sur une surface plane
- Ne jamais poser un objet à proximité du bord d’un établi ou d’une étagère
- Vérifier la stabilité des charges empilées
Et pour cause, ce sont souvent les petits oublis qui provoquent les grosses blessures.
Portes qui claquent : un risque mécanique trop souvent négligé
On ne s’en méfie pas forcément, mais une porte qui claque violemment peut faire bien plus que du bruit. Dans les ateliers, les cuisines collectives, les entrepôts ou les zones de livraison, une porte lourde, un battant métallique ou une trappe mal contrôlée peut provoquer des blessures sérieuses, notamment aux doigts et aux mains.
Et ce risque n’est pas réservé aux environnements industriels Il suffit d’un courant d’air, d’une fermeture automatique mal réglée ou d’un geste imprudent pour qu’un accident se produise… en quelques secondes.
Quand la porte devient un danger
Une porte qui se referme trop vite, c’est un danger silencieux. Dans le feu de l’action, on ouvre, on ferme, on passe sans faire attention… et parfois, la porte se referme toute seule, trop vite, trop fort. Ce mouvement brutal peut coincer les doigts dans la charnière, le chambranle et entre les vantaux dans le cas d’une double porte.
Les conséquences peuvent aller de la contusion légère au sectionnement partiel du doigt, voire à des lésions tendineuses ou articulaires nécessitant une intervention médicale.
Les causes les plus fréquentes
Quand un simple défaut mécanique devient une source d’accident, il est essentiel d’identifier les origines du problème pour mieux les anticiper.
- Fermeture automatique mal réglée, trop rapide ou sans système d’amortissement
- Portes lourdes (métal, bois massif, vitrées) sans frein de fin de course
- Trappes ou battants non stabilisés qui se referment sous leur propre poids
- Absence de protection mécanique sur les zones à risque (notamment au niveau des gonds ou des charnières)
Des solutions concrètes et faciles à mettre en place
La prévention passe par une combinaison d’équipements adaptés et de bons réflexes. Voici les leviers efficaces pour réduire ce risque au quotidien.
1. Installer des systèmes anti-pince-doigts
Ces protections, souvent en caoutchouc ou en plastique souple, se fixent le long des charnières ou sur les côtés exposés des portes. Elles empêchent tout contact direct avec la zone de pincement.
Ces systèmes sont adaptés aux zones de fort passage : cuisines, ateliers, cantines, écoles, etc. Déclinables en version souple, rigide ou transparente, selon les usages, ils peuvent être installés sur des portes neuves ou existantes.
2. Poser des vérins ou dispositifs anti-claque
Un vérin de fermeture amorti permet à la porte de se refermer lentement, même si elle est poussée avec force ou si un courant d’air intervient. Ce dispositif protège à la fois les personnes et la porte elle-même pour réduire l’impact sonore, protéger les extrémités et allonger la durée de vie de la porte en évitant les chocs répétés.
3. Sensibiliser le personnel aux bons gestes
La technique ne fait pas tout. Les bons gestes au quotidien sont tout aussi essentiels
- Ne jamais refermer une porte d’un geste brusque
- Tenir le battant jusqu’à la fermeture complète
- Signaler toute porte instable ou qui claque anormalement
- Protéger les enfants ou collègues fragiles dans les zones à risque
Une simple formation de quelques minutes suffit à faire prendre conscience du risque.
Roues en mouvement : écrasements au sol et incidents de cohabitation
Dans un atelier, un entrepôt ou une zone logistique, les équipements roulants sont partout : chariots élévateurs, transpalettes, dessertes, véhicules de service… Ils facilitent les déplacements de charges, optimisent la productivité, mais peuvent vite devenir dangereux si leur usage n’est pas encadré.
Un angle mort, une marche arrière mal anticipée, un sol encombré… et c’est un pied écrasé, un câble sectionné, ou un opérateur coincé entre un engin et un mur. Ce type d’incident est fréquent… et trop souvent sous-estimé.
Des circulations mal anticipées peuvent coûter cher
La cohabitation entre piétons et engins roulants exige une attention constante. En l’absence de règles claires et d’anticipation, les accidents sont presque inévitables.
Les équipements roulants ne pardonnent pas les imprévus : leur poids, leur inertie et leur champ de vision parfois limité les rendent particulièrement redoutables dans un environnement actif.
Que ce soit une desserte poussée à la main ou un chariot élévateur motorisé, un simple mauvais positionnement peut provoquer un accident grave.
Les risques fréquents à connaître
Identifier les situations à risque permet d’agir rapidement. Voici les incidents les plus courants liés aux équipements roulants.
- Écraser des câbles, des flexibles ou des tuyaux au sol :
- Ces éléments sont souvent temporaires, visibles mais vulnérables. Un passage d’engin peut les endommager, provoquer une panne, une fuite de fluide, voire un arrêt de production
- Rouler sur le pied d’un opérateur
- Ce type d’incident reste parmi les plus fréquents. Il suffit d’un petit transpalette manuel ou d’un virage trop serré d’un chariot pour provoquer une fracture, un hématome profond ou un écrasement partiel du pied
- Coincer un opérateur entre l’engin et une paroi fixe
- Dans les zones étroites ou mal balisées, un opérateur peut être piégé entre une palette et un mur, ou entre deux engins en mouvement
Tous ces cas ont un point commun : ils peuvent être évités avec de meilleures pratiques et une meilleure organisation des flux.
Préconisations techniques pour limiter les accidents
La prévention passe par une combinaison d’équipements adaptés, de balisage clair et de formation pratique. Voici les leviers efficaces à actionner
1. Protéger les installations au sol
Un câble au sol est une faiblesse. Il faut le traiter comme un point sensible à sécuriser.
- Installer des passe-câbles renforcés, en caoutchouc ou en plastique dur pour couvrir les zones de passage
- Prévoir des protections visibles (jaune/noir, pictogrammes) pour éviter qu’un opérateur ne marche dessus ou qu’un engin ne les détériore par inadvertance
2. Renforcer la protection individuelle
Quand un engin passe trop près, seul l’équipement peut faire la différence entre une frayeur et une blessure grave. Les équipes doivent
- Porter des chaussures de sécurité normées, avec
- Coque anti-écrasement (minimum norme S1P ou S3 selon le terrain)
- Semelle rigide anti-perforation
- Bande anti-dérapante pour éviter les glissades au moment critique
3. Organiser les déplacements : balisage et séparation
Un espace de travail bien organisé, c’est moins de stress et moins d’accidents. Pour cela, il faut :
- Délimiter des zones de circulation claires et visibles, avec peinture au sol, fléchage directionnel, barrières physiques si nécessaire
- Séparer les flux piétons / engins autant que possible, surtout dans les zones de manœuvre ou de livraison
4. Former les utilisateurs aux bons réflexes
Un engin bien conduit, c’est surtout un conducteur bien formé. La formation permet de
- Sensibiliser à l’anticipation des obstacles
- Former au freinage progressif, à la vigilance en marche arrière et à l’usage des avertisseurs sonores
- Apprendre à lire son environnement en permanence en intégrant les angles morts, les zones à risque et les autres usagers
Les autres sujets sur les accidents d’écrasement au travail
- Statistiques et tendances des accidents d’écrasement au travail
- Réglementations et obligations légales en matière de prévention
- Solutions et innovations pour prévenir les risques d’écrasement au travail
Les risques professionnels individuels
Sources
Commentaires
Laisser un commentaire